Poly Processing Chemical Storage Innovations
You don’t get to be the leader in chemical storage tank manufacturing unless you’re also constantly innovating better solutions. Poly Processing is constantly pushing the envelope to develop new products and to improve existing chemical storage solutions.
Not only do we continually strive to introduce new solutions that no other tank manufacturer can offer, we also aim to develop new products that outperform our current ones. It’s not unusual to find content on our site that’s been updated with new innovations and product information.
Poly Processing custom manufactures cross-linked polyethylene storage tanks to fit the unique needs of our customers. We’ll help you design a chemical storage solution that’s manufactured with our own innovations—just the ones you need, and none that you don’t.
Poly Processing is a leader in building innovative solutions to complex chemical storage challenges. Far beyond simple plastic tanks, we have developed a fleet of products that address a wide range of specific issues related to chemical storage. The result for your business is an ease of use, increased safety and environmental care, easy tank maintenance, and extended tank longevity.
Discover how we’ve set ourselves apart and the groundbreaking technology we’ve produced—explore each of Poly Processing’s industry-leading storage tank innovations.
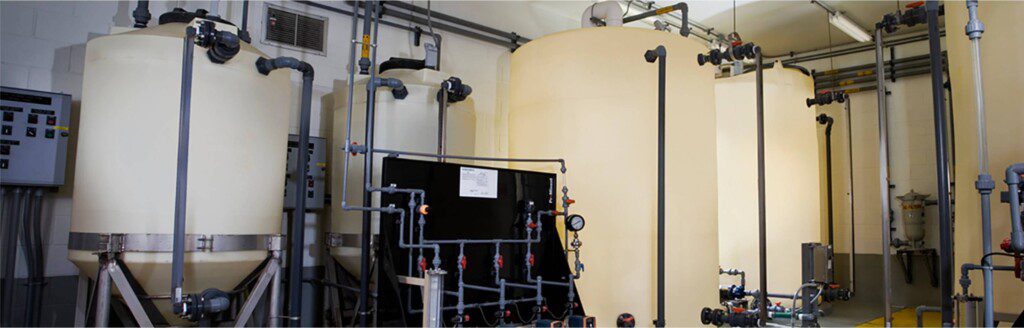
NSF/ANSI 61 Certified Tank Systems
NSF/ANSI 61 is a set of national standards that relates to water treatment. It establishes stringent requirements for the control of equipment that comes into contact with either potable water or products that support the production of potable water. The tests vary from a basic cold water test at different pH levels to the more challenging chemical certification.
Many manufacturers have certified tanks, but their fittings and gaskets may not be NSF/ANSI certified. Poly Processing is the only chemical storage tank manufacturer to take a full system approach to NSF approval. We supply an entire tank system, including fittings, gaskets and specific tank colors, that are certified for NSF/ANSI 61.
See More Details On Our NSF/ANSI 61 Certified SystemsDownload Our NSF-61 Guide
In this guide, we'll highlight specific state regulations and explain what you need to do to comply with them.
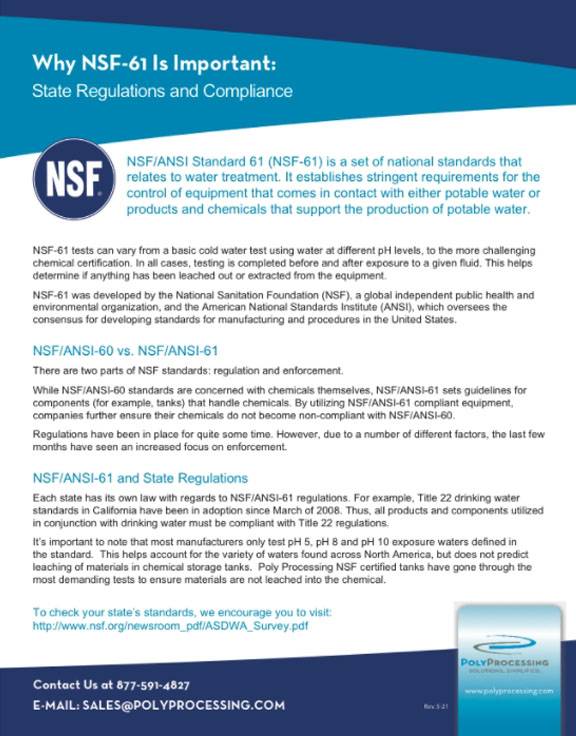
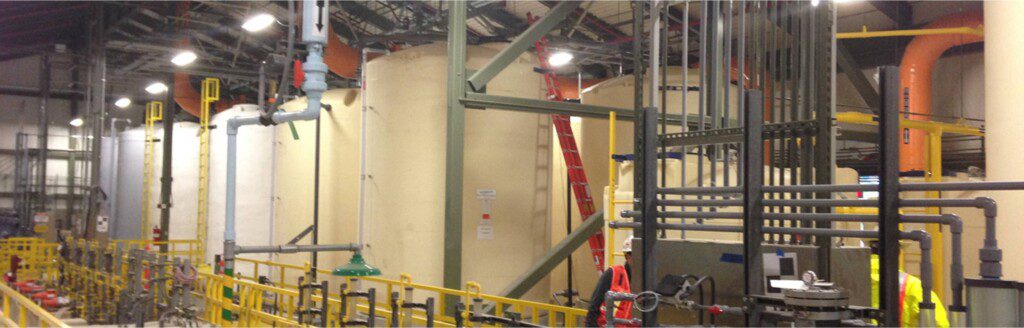
Cross-Linked Polyethylene (XLPE) Tank
Not all high-density polyethylene tanks are created equal. Although they sound nearly identical, linear polyethylene and cross-linked polyethylene (XLPE) chemical storage tanks have significant differences. Those differences could impact your organization’s bottom line, your people’s safety, and the operations of your facility.
The four most important factors of high-density linear tanks and cross-linked tanks include:
- Environmental stress crack resistance/notch sensitivity
- Long-term hydrostatic strength
- Toughness and Durability
- Useful Life
Compared to linear polyethylene, XLPE provides:
- 10-20 times the environmental stress crack resistance
- 10 times the molecular weight
- 3-5 times the impact and tensile strength
Because XLPE has a significantly longer life and less financial impact in case of tank failure, the total useful life of cross-linked polyethylene is significantly better for your bottom line.
See More Details On Our XLPE Tanks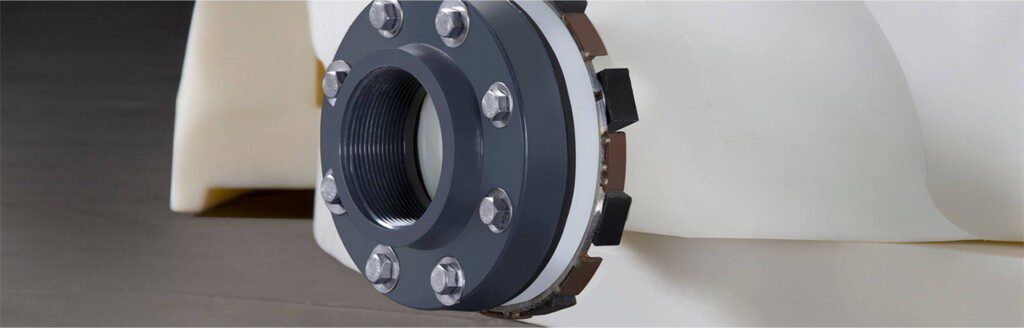
Integrally Molded Flanged Outlet® (IMFO®) Tank
Poly Processing’s Integrally Molded Flanged Outlet (IMFO) Tank is a homogenous full discharge flange system that is molded as part of the tank while it’s being manufactured. As a result, the outlet is a fully integrated, stress-free part of the tank. The flange is created from the same material as the tank, and it’s not a fitting or accessory that’s added during post-production.
An IMFO Tank delivers a number of benefits to a chemical tank storage system that a metallic insert simply can’t offer. These include:
- Full tank discharge, because the flange is at the bottom of the sidewall, below the tank knuckle radius. There’s no longer a need to enter the tank for cleaning.
- Enhanced long-term performance and fuller useful life of the tank, since the flange doesn’t compromise the tank’s hoop integrity or structural design.
- No connection points to provide opportunities for leaks as the tank ages.
- Complete flange face protection is available in aggressive oxidation environments. The antioxidant OR-1000™ system can protect the discharge components and give you greater useful life.
- Highest amount of static head pressure. The IMFO’s design brings you the highest net positive suction head (NPSH) of any vertical non-coned tank on the market.
- Any required maintenance is simple and hassle-free. Unlike metallic inserts, the flange extends away from the tank wall and the entire flange system is external with easy hardware access from outside the tank.
- There are no chemical compatibility issues like the ones you may encounter with metallic inserts. If the chemical is safe in a crosslinked polyethylene tank, it’s safe discharging out of the IMFO system.
Download Our IMFO Guide
The IMFO®, Integrally Molded Flanged Outlet, product guide contains details on our unique system that helps minimize the hazards associated with traditional vertical tank maintenance.

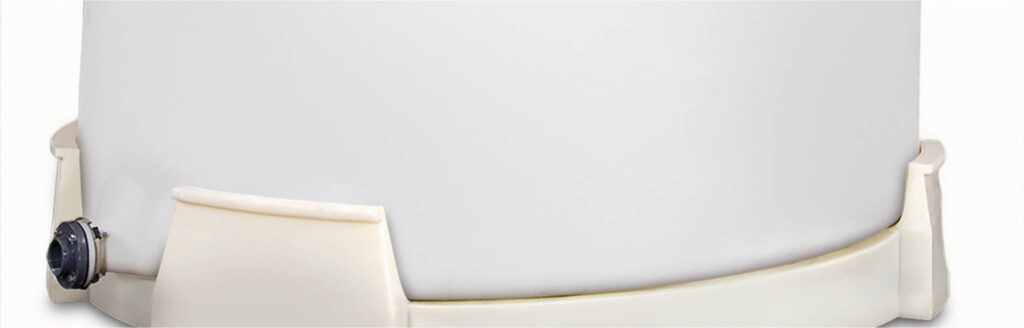
Sloped Bottom Vertical IMFO® Tank
The Sloped Bottom IMFO tank is a specially designed IMFO tank with a sloped bottom. This version excels when it comes to discharging heavier materials such as FOG (fat, oils, and grease) or sludge like materials. The sloped bottom creates an additional gravity feed that makes it easy for substances to discharge completely, leaving no residue or sludge to build up.
The Sloped Bottom IMFO Tank is more cost effective than cone-bottom tanks, and it comes with fewer drawbacks such as the need for special mounting on metal support frames.
Cleaning is simple, because there is no need for a confined-space entry. Instead, the sloped bottom tank can be cleaned from the top manway, or with a spray ball installed in the dome. It’s a solution that’s much safer for your personnel, and more cost-effective.
See More Details On Our Vertical IMFO Tanks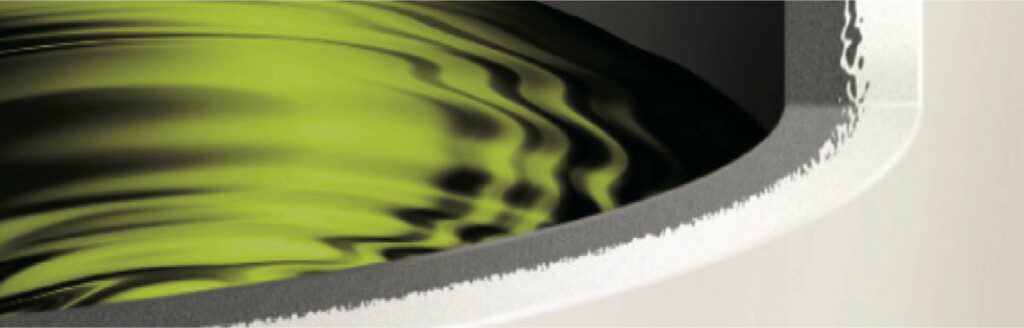
OR-1000™ System
If you have aggressive oxidizing chemicals that you’re storing, Poly Processing has you covered. Our OR-1000 System adds an antioxidant barrier between aggressively oxidizing chemicals and your high-density crosslinked polyethylene tank.
The OR-1000 System is specifically formulated to resist oxidation and give you greater tank life. The outer surface is made of XLPE and offers superior strength, longevity, and chemical resistance. The inner surface provides an additional antioxidant resin barrier. The two surfaces are molecularly bound together during tank production, creating a truly seamless bond between the XLPE and the inner surface of the polyethylene tank.
The OR-1000 System addresses the chemical resistance of oxidizing chemicals for 15+ years. The system isn’t your typical resin. In fact, it has four times the antioxidizing power, compared to other commercially available resins. This high level of antioxidant additive ensures greater longevity for your initial investment.
See More Details On Our OR-1000 SystemDownload Our OR-1000™ Guide
Poly Processing’s exclusive OR-1000TM system was specifically designed to address the aggressive oxidation effects of sodium hypochlorite, sulfuric acid and hydrochloric acid by adding an additional chemical barrier between XLPE and the chemical.
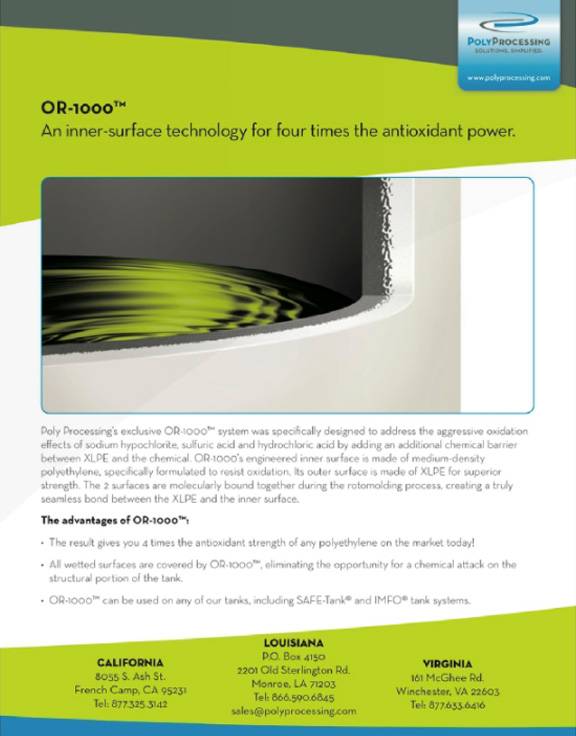
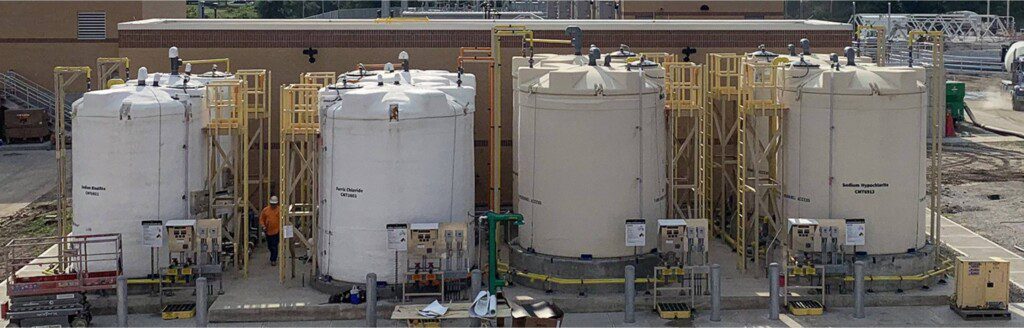
SAFE-Tank® Double Wall Tank System
Poly Processing’s innovative SAFE-Tank® double wall storage and containment system, the “tank within a tank,” provides you with a cost-effective solution that offers peace of mind and environmental care.
The high-density crosslinked polyethylene SAFE-Tank alleviates the need to build large, high-maintenance concrete containment areas. In the event of a spill, the SAFE-Tank’s all-in-one design features a protected containment area that safely isolates reactive chemicals, protects your employees from harm, and protects you from environmental remediation, all within the footprint of a standard vertical tank.
And because the containment area is enclosed, your spilled chemical is protected from water and contaminating debris that can enter traditional secondary containment areas.
The SAFE-Tank Double Wall Tank System:
- Provides at least 110% secondary containment.
- Equalizes spilled liquid and allows the chemical to be used until it is convenient to repair the tank if necessary.
- Is ideal for chemicals like sulfuric acid that can have dangerous exothermic reactions to water.
- Eliminates the expense, cost, and maintenance of secondary concrete containment.
- Minimizes the system’s footprint by providing secondary containment in a more compact way.
- Allows you to add a bellows transition fitting in order to maximize your SAFE-Tank system’s performance.
Download SAFE-Tank® Guide
Poly Processing's SAFE-Tank® double wall tank system is a "tank-within-a-tank" that provides secondary containment to avoid the damaging of equipment or property, loss of chemicals, or injury to employees in the event of a spill.
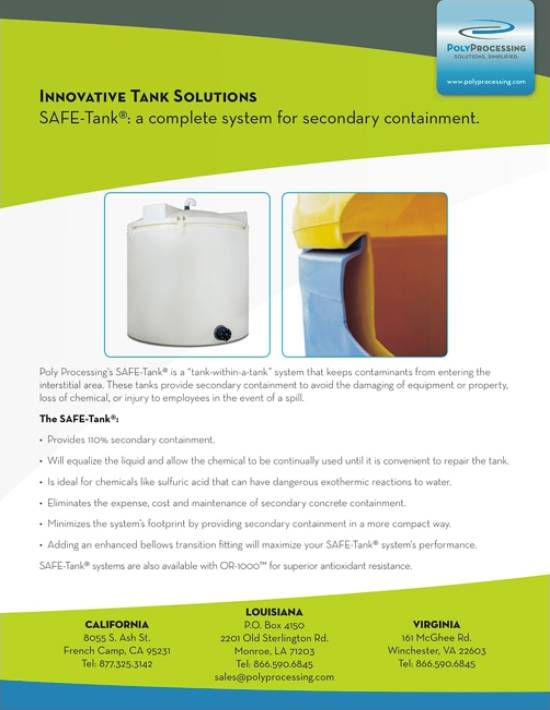
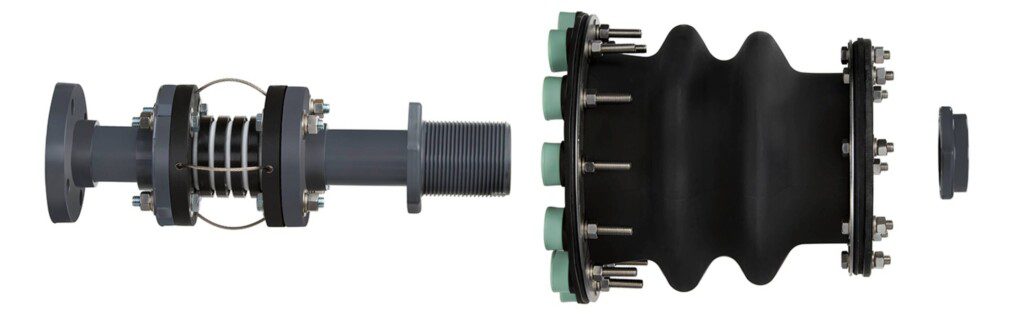
Poly Processing’s Bellows Transition Fitting
When you install a double wall chemical storage system like the SAFE-Tank with a sidewall fitting, it may be important to also install a Bellows transition fitting. The Bellows transition fitting has a flexible expansion joint that is in line with the outlet pipe that runs through both the inner and outer walls of the SAFE-Tank.
The transition fitting fully contains both the fitting and piping from the inner tank, through the outer tank, to the outlet. If the fitting or any of the seals becomes overstressed and fails, the leak is contained inside the bellows. The leaked chemical flows back to the containment space between the inner and outer SAFE-Tank walls.
See More Details On Our Bellows Transition Fitting
The B.O.S.S. Fitting®
This one-piece sure-seal fitting prevents leaks and adds value to your tank installation. Its one-piece design reduces the seal point to a single gasket, and its polyethylene construction ensures chemical compatibility. The B.O.S.S. Fitting’s back ring design reduces stress on the fitting and makes it three times stronger than similar plastic fittings.
This unique fitting:
- Is constructed of polyethylene for chemical compatibility with your tank.
- Has an innovative backing ring design to reduce stress on the fitting and make it three times stronger than plastic fittings.
- Is easy to maintain, since the pipe connection is extended beyond the sidewall of the tank.
- Is available in 1, 2 and 3 inches in diameter with a PVC or CPVC socket connection.
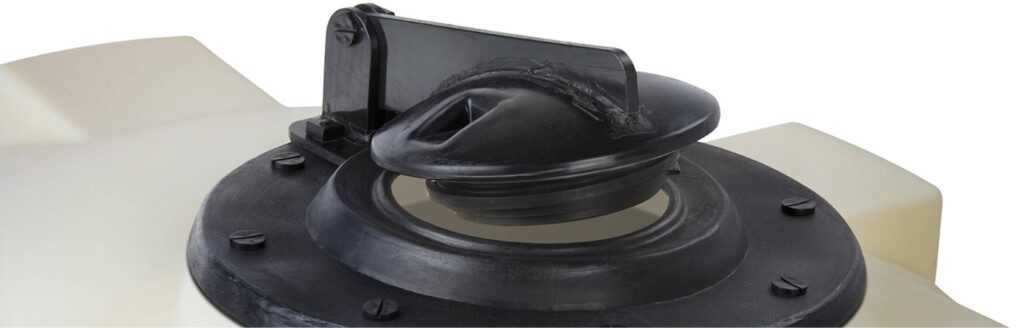
SAFE-Surge® Manway Covers
Proper venting of polyethylene chemical storage tanks is vital for safe operation — it’s also critical for maximizing a polyethylene storage tank’s useful life.
Poly Processing’s SAFE-Surge manway covers ensure that your tank maintains the proper actual cubic feet per minute (ACFM) at all times – even in the event of air surges that can’t be handled by primary venting. This system was designed specifically for pneumatic-filled tanks.
SAFE-Surge® Manway Covers:
- Release at a 6-inch water column to prevent over-pressurization.
- Feature an easy inspection port.
- Are available for 19- and 24-inch manways.
- Are never to be considered part of your primary venting.
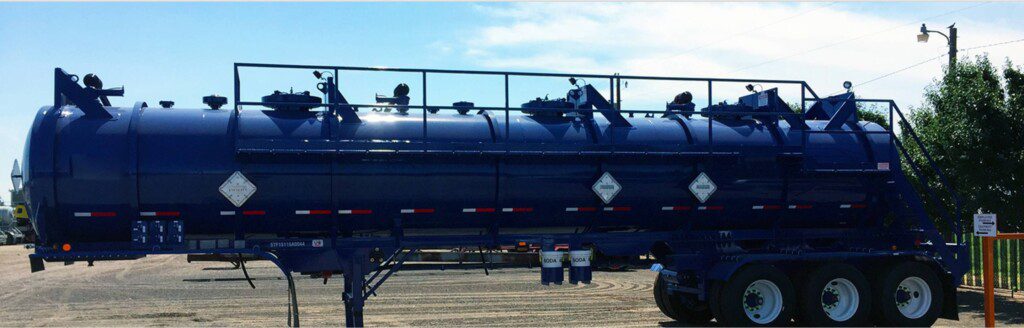
PolyGard™
PolyGard is a seamless, corrosive-resistant polyethylene lining system that serves as a barrier between a steel tank and the chemical it’s storing – and it protects your vessel even in the harshest of conditions. Use PolyGard to line steel vessels for increased performance and better chemical storage solutions.
The robust, seamless lining system prevents highly oxidizing chemicals such as sulfuric acid, hydrochloric acid, ammonia, and other compounds from attacking the steel surface, greatly extending the life of your tank.
See More Details On Our PolyGard Innovation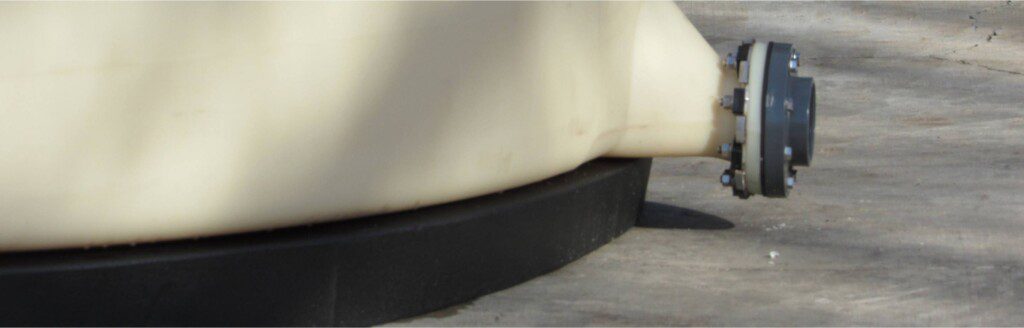
PolyBase
Poly Processing’s stronger-than-ever chemical tank pad, PolyBase, is engineered to handle more pressure and larger tanks. We have two types of PolyBase systems available: rotationally molded PolyBase systems for our IMFO Tanks, and an innovative structural polyurethane foam based IMFO PolyBase option.
The polyurethane foam PolyBase outperforms our rotationally molded line of pads, supporting a broader spectrum of chemical storage applications. It is available for our IMFO Tanks as well as our slope bottom IMFO Tanks.
See More Details On Our PolyBase Innovation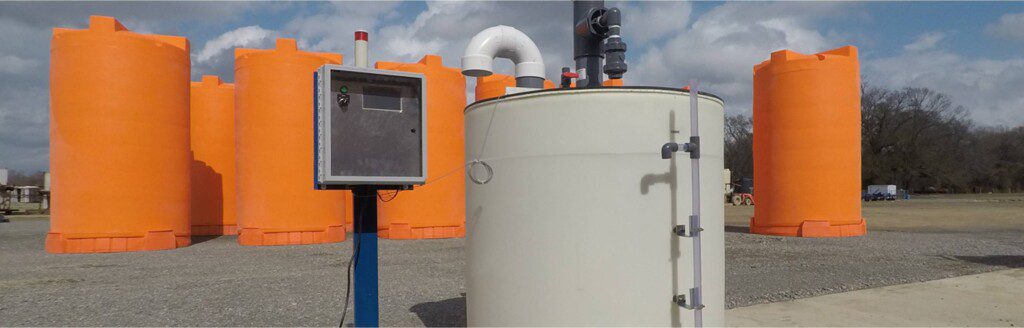
PolyScrub Basic™ and PolyScrub Plus™
Fume scrubbers are installed to remove or neutralize the harmful substances emitted from combustion, or in this case, the storage of chemicals.
We have the ability to produce simple to more complex scrubbers to go with our chemical tank systems based on your specific needs. Our standard scrubber PolyScrub Basic™ consists of a submerged plenum, which allows fumes to bubble through a water bath. It has manual valves and no electronics, so there’s no need for a power supply.
We also have the ability to supply the automated PolyScrub Plus system. This system includes the PolyScrub Basic but also includes electronic components to monitor scrubbed air and give you the automation you need for maintaining a neutral pH system.
Poly Processing scrubbers are ideal for:
- Applications where fumes or odor are problematic
- Hydrochloric acid, acetic acid, and ammonium-based products to eliminate toxic fumes
- Ferric Chloride to address environmental issues
- Maintaining cost-effective solutions, compared to other alternatives
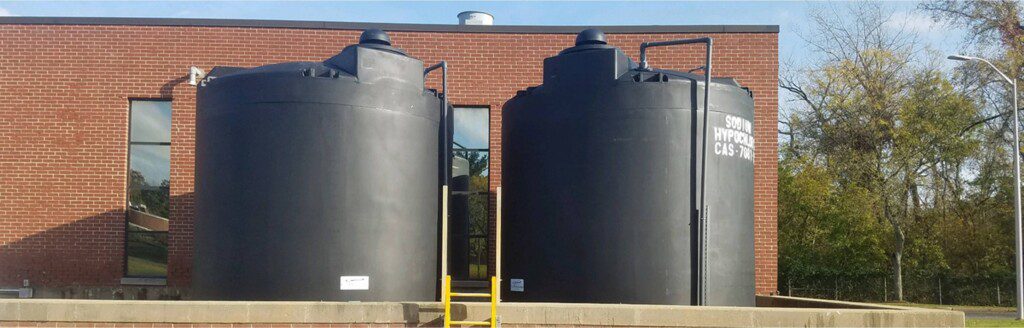
Poly Processing Is Your Solution to Any Chemical Storage Challenge
Each of these innovations is unique to Poly Processing. They were developed with you, the customer, in mind. We’re constantly striving to meet your chemical storage needs and to create better solutions that are safer and give you longer useful life.
Known as the leader in crosslinked polyethylene chemical tanks, Poly Processing is dedicated to storage safety, as well as operational- and cost-effectiveness. We have worked to raise the standards of the industry and continually develop new and better storage systems that are based on client feedback and over 50 years of real world experience.
While Poly is known for its technological innovations, it is also known for its human approach to business and service. Here, every phone call is answered by a person, not a machine – and customer service is at the heart of all we do.